Freightweek at busy IATA World Cargo Symposium
0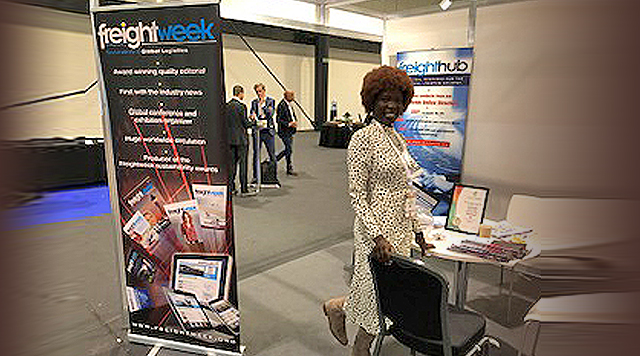
Freightweek offers extensive range of services
at busy IATA World Cargo Symposium at ExCeL London
Freightweek offers extensive range of services
at busy IATA World Cargo Symposium at ExCeL London
PCN are pleased to announce Al-Marasi International are new members in Iraq.
The company is 15 years old, and their project logistics services include complete management, route surveys & heavy lift engineering, OOG cargo handling & transport, warehousing, customs clearance and governmental assistance. They are ISO certified with locations in Basra and Baghdad.
Managing Director, Ali Majid Sabah: âThe Al-Marasi team consists of an experienced group of logistics experts working together to offer well-designed solutions for the diverse tasks required for the successful management, control and execution of project cargo. Covering all modes of transport from sea, land, air and multimodal, we now have a long history of dealing with different types of abnormal and OOG cargo for various industries including large power plant projects with generators & transformers, oil field equipment & turbines, heavy machinery, agricultural cargo and vehicles.â
âAll cargo is handled with the maximum care and the highest level of efficiency and safety, always following a well-prepared plan based on extensive studying of cargo requirements & specifications, HSE rules, route surveys and engineering reports.â
The post PCN announces AL-Marasi as members in Iraq appeared first on Project Cargo.
Mammoet has announced a fixed jib configuration for the SK6,000 that will allow offshore wind developers to reach deeper waters and significantly cut the cost of floating wind assembly.
Fixed bottom turbines and their foundations are growing fast, so that projects can be built further from the coast where winds are stronger and greater yields can be achieved. As a result, jackets and monopiles are reaching both the height and weight capacity of the worldâs largest cranes.
As the industry moves towards 20MW turbines, floating wind components continue to grow in size and weight. This increases the need for a modular approach, to speed up the construction process and allow developers to install more floating turbines in reduced weather windows.
With the launch of the SK6,000, Mammoet is providing the next generation crane needed to install next generation turbines. Now, with its existing, patented, fixed jib configuration, lifts of 3,000 tonnes at 220m height become a reality.
Whatâs more, this new configuration means that the crane can load out floating foundations using its main boom, then immediately use its fixed jib to assemble the turbine tower. No reconfiguration will be necessary between scopes, further improving build efficiency.
Mammoet technical expert Jeremy Haylock explains:âWe donât look at the SK as âjustâ a crane, but we look at it as a system as well. If you look at the SK of today compared to when it was first launched, it has evolved considerably.
This isnât a surprise because it was always the basis of our original design philosophy, and we wanted to develop a product that would be scalable and agile. Because the world is developing so quickly, and the changes around us are so vast, our aim was to deliver a product that would allow us to grow in real time with our customersâ.
The SK6,000 fixed jib is just the latest evolution in a crane series that allows small adjustments to have a large affect on performance, avoiding the need to research, develop and fabricate an entirely new crane.
Haylock continues: âAs with every part of the SK, when we developed the fixed jib, we wanted to include room for growth. With the SK6,000 jib we are employing that additional capacity through small adjustments to the original design.
The fixed jib is fully forward and backward compatible through the SK series, meaning our customers can realize its potential, regardless of the application.â
The new jib design will be incorporated into future Mammoet offshore wind project proposals, for deployment to a suitable project at the first possible opportunity.
The post Mammoet announces fixed configuration for the SK6, 000 appeared first on Project Cargo.
Express Global Logistics (EXG), member to the Worldwide Project Consortium (WWPC) in India, successfully completed the movement of galvanised transmission line towers and parts for one of the largest infrastructure construction companies.
The 4740 tons of transmission line towers were shipped via six barge trips. The total distance covered for each lot from the shipperâs works to the final site in Bangladesh was about 3110 km.
The transport at origin had various challenges and one of the major ones was arranging 207 trailers for the movement of cargo from shipperâs works to the port without any delays as the barging windows at load port were short and precise. EXG seamlessly completed export clearance, port handling, loading on a barge at origin so as to avoid any vessel detention or port storage charges. The loading on barges was done under the supervision of EXGâs well experienced team ensuring no damage to the cargo. A swift discharge at Bangladesh due to timely import documentation and clearance ensured smooth port handling and delivery at the final site by EXGâs team.
The successful delivery was possible only as a result of extensive and precise transport planning. Seamless handling of bundled cargo was done to maximize the space on the barges ensuring absolute stability for sea voyages.
The thorough sequencing of cargo while loading ensured smooth and proper segregation of cargo to the destination as the deliveries were planned to more than nine separate locations across Bangladesh.
The post EXG completes transportation to Bangladesh appeared first on Project Cargo.
Hiab, part of Cargotec, launches the total service solution; HiPerform intelligent solutions for optimised performance at IAA TRANSPORTATION.
HiPerform uses intelligent solutions and remote services to optimise equipment performance, uptime and safe operation. Hiabâs market-leading number of connected units has helped the company to develop unique insights and solutions for the total offering that comprises Hiab HiConnect, Hiab Uptime and Hiab ProCare providing connectivity, real-time monitoring and diagnostics, as well as tailored service agreements.
Hiab HiConnect is a connected solution that gives the customer access to real-time insights about the condition of their equipment, to help them to further increase efficiency, productivity and operator safety. Customers can monitor status, plan service and improve operation from whole fleets down to single units. Hiab HiConnect is available in two levels: HiConnect Insights and HiConnect Premium.
Hiab Uptime comprises real-time remote monitoring and diagnostics. Equipment with Hiab Uptime is connected to Hiabâs Remote Monitoring Center that can detect critical alerts. When an alert is detected, Hiab immediately informs the designated point of contact to enable the fastest time-to-fix available in the market. Every month, Hiab delivers a report with a summary of all the monitoring and remote support activities taken, as well as recommendations based on the equipment status, performance and safety. Hiab continues to invest in this area, developing further remote and predictive insights. Hiab Uptime is currently available in selected markets only.
Hiab ProCare is a flexible, multilevel service contract. With scheduled and proactive maintenance, equipment retains the high quality which was invested in from the start. Equipment covered by Hiab Uptime has the possibility to be monitored in real-time by engineers at the Hiab Remote Monitoring Center. If they identify any technical, safety or operational issues, they will contact the customer to resolve the problem. Customers will also receive a monthly report based on the equipment status, performance and safety, complete with our recommendations. Hiab ProCare is available in three service levels: Total R&M, Essential, and Extended Warranty.
Rory Pedd, Vice President, Sales & Product Management, Hiab comments: âOur new HiPerform offering provides our customers with the daily insights, maintenance and care for their equipment. The customer relationship doesnât stop at the point of delivery, with HiPerform, we work with customers and their equipment to ensure optimal performance and safety at every point in its use. With tailored performance reports and insights, our customers can easily identify how to best maximise the use of their equipment and the job at hand to further keep their promises to deliver on time, every time.â
âHiabâs strategy is to continue to lead the digitalisation of the load handling industry. We want our customers to experience the highest uptime, the safest operations and the best productivity. To fulfil this, we will continue to invest in digitalisation to support our customer needs, to support our service partners and to be the leading solution provider,â says Michael Bruninx, Senior Vice President, Services, Hiab.
He adds: âHiab HiPerform is the overall portfolio of exciting digital solutions like HiConnect, Hiab ProCare, Hiab Uptime and the Hiab Simulator. We established the Hiab Customer Experience and Remote Monitoring Center to perform diagnostics, monitoring and services remotely. Our customers benefit from our large connected installed base which enables us to develop market-leading solutions in the HiPerform offer based on artificial intelligence, advanced data science and analytics.â
In Q4 2022, Hiab will launch Hiab Simulator to more markets to support customers with the fastest, less costly, most effective training solution for onboarding new operators and to further enhance operator performance.
The post Hiab launches HiPerform total service solution appeared first on Project Cargo.
Rhenus UK has opened the doors to a new logistics centre near Heathrow Airport, a major investment designed to considerably strengthen its offer across life sciences and healthcare, full vehicle logistics and its air and ocean freight operations.
More than 80 customers, suppliers, partners and colleagues joined Rhenus UK to celebrate the opening of its new 58,000 square feet handling facility located in Ashford, just four miles from London Heathrow airport. The site will be the new home for the brand-new specialist pharmaceutical, life sciences and healthcare centre, the expanding Full Vehicle Logistics team, which manages the global transport of vehicles, as well as a new airfreight gateway.
Spencer Davern, UK Managing Director at Rhenus Air & Ocean UK said: âOur investment in this state-of-the-art facility and in our specialist teams has been designed to meet the future needs of our broad spectrum of customers to ensure the safe and secure handling of pharmaceutical and medical products. We are proud to support our customers so they can help patients to the utmost with the launch of our new Heathrow site.â
Rhenus UK is also announcing an exciting initiative in partnership with Cancer Research UK, pledging to donate a penny to the charity for every kilogram moved through the new facility.
âThe facility is temperature controlled, which means it requires the installation of heating, ventilation and air-conditioning pipes or dire-jet sock systems that run across the warehouse ceiling,â Davern continued. âUsually these âsocksâ are blue, but our team has decided to make them pink to raise awareness among staff and visitors to the site or our commitment to raising money for the charity. To celebrate our fundraising Pink Socks Programme, each visitor to our open day was gifted a pair of pink socks!â
The new life sciences and healthcare division will act as a one-stop-shop for all import and export logistics, offering a white glove service for temperature-controlled storage and distribution from end to end.
The Full Vehicle Logistics team will provide a dedicated service using a mix of air, ocean and road transport to move finished vehicles around the world for individuals, dealerships and OEMs.
The new air freight gateway is fully equipped with the latest X-Ray screening equipment, and will promote more sustainable airfreight by consolidating shipments, helping Rhenus and its customers to reduce their carbon footprint.
The centre was opened by Tobias König, Global CEO Rhenus Air & Ocean. He commented: âThis new-build project represents a significant investment for Rhenus, demonstrating both our commitment to this sector of the market and the further growth of our operations in the UK and across Europe, while reflecting our global expansion plans. As a result of strong customer demand, we will continue to invest in and expand our life science and healthcare facilities worldwide, keeping pace with the needs of the market.â
The post Rhenus hub opens near Heathrow appeared first on Project Cargo.
Siemens Gamesa again takes strong command of circularity within wind turbine blades, launching its RecyclableBlade for onshore wind power projects.
This milestone is set to propel the activities that make wind energy even more sustainable, creating a fully circular sector.
The Siemens Gamesa RecyclableBlade for offshore was brought to market in only 10 months: launched in September 2021 and installed at RWEâs Kaskasi project in Germany in July 2022. The corresponding onshore solution is now ready for customers to employ at their onshore wind sites. Further development by Siemens Gamesa and partners ensure full compatibility with the product and process requirements for onshore blades.
âLaunching our RecyclableBlade for onshore sites is another outstanding achievement from our dedicated professionals. The concept was always foreseen to encompass solutions for offshore and onshore, and weâre pleased to now provide them commercially to our customers in both market segments,â said Jochen Eickholt, CEO of Siemens Gamesa.
Both onshore and offshore markets around the world continue to set ambitious targets for installed wind power capacity, with the demands for ensuring recyclable solutions gaining more importance. Turbine sizes, and in turn their blades are growing rapidly, making it even more imperative to find solutions to ensuring their circularity. With the RecyclableBlade for onshore, Siemens Gamesa continues to put action behind its Sustainability Vision towards 2040 where a core target is fully recyclable wind turbines by 2040 at the latest.
âWe are driving the wind industry towards full circularity with our commitment to make wind power as sustainable as it can be at every stage of its lifetime. Together with our customers and our suppliers, we want wind power solutions from Siemens Gamesa to continue to help countries around the world meet their net zero carbon emission goals,â said Tim Dawidowsky, Siemens Gamesa COO and Chief Sustainability Officer.
The post SG announces RecyclableBlade for onshore projects appeared first on Project Cargo.
Total Movements, member to the Worldwide Project Consortium (WWPC) in India, reported about a successful multimodal transport of a 730 ton heavlift cargo on the West Coast of India consigned for a refinery project in Thailand.
The cargo with a width of 8 meter and weighing 730 ton was moved from the supplierâs plant to the load port in India.
A spokesperson for Total Movements stated: âRoad transportation from the supplierâs works to the nearest jetty, barging to the nearest seaport on the west coast and feeding alongside the vessel were all part of our scope. The nominated jetty was a tidal jetty, due to which the required barging operation had to be accomplished in a particular time slot, which posed a significant challenge. The cargo was rolled on to the barge, lashed and secured as per the planned method statement and safely barged to the load port and fed alongside the designated chartered ocean vessel for the voyage to Thailand.
Our engineering/execution team made site visits and detailed discussions with multiple stakeholders to execute this movement in a flawless manner.â
The post Total Movements reports successful transport in Thailand appeared first on Project Cargo.
MacGregor, part of Cargotec, has received a significant order for delivering container lashing systems for twelve 23,500+ TEU container vessels for Hapag-Lloyd.
The vessels will be built at Daewoo Shipbuilding & Marine Engineering (DSME) in South Korea.
The order was booked into Cargotecâs 2022 third quarter orders received. The vessels are scheduled to be delivered to the owner between the second quarter of 2023 and the fourth quarter of 2024.
âCargo system plays a very important role in the efficient operation of the container ship. Hapag-Lloyd and MacGregor have worked together closely and developed the optimum cargo system for this vessel series to ensure the best cargo efficiency. Placing this order with MacGregor was the first choice for us,â says Lutz-Michael Dyck, Senior Director, Strategic Asset Projects, Hapag-Lloyd.
âHapag-Lloyd is a highly appreciated and strategic customer for MacGregor. Over the years we have worked together closely to find ways to improve the cargo efficiency on existing ships and newbuildings. In this project, we have been collaborating on concept design and cargo system configuration from the very early stages. I am very proud that Hapag-Lloyd trusted us with this order,â says Magnus Sjöberg, Senior Vice President, Merchant Solutions, MacGregor.
Hapag-Lloyd is currently the worldâs fifth largest container carrier with 253 container ships totaling a capacity of 1.8 million TEU. Hapag-Lloyd is known for its dedication to efficiency and minimizing environmental impact.
The post MacGregor to supply systems for Hapag-Lloydâs container vessels appeared first on Project Cargo.
KGE Baltic, our members from Latvia, were recently nominated by Lysander Shipping to transport a large quantity of ISO tanks from Jebel Ali to Qarshi, Uzbekistan, with the empty tanks being delivered back to the lessor in Antwerp.
The specific cargo involved with this shipment included twenty-six 20 ft ISO SOC tanks. It was a multimodal shipment which travelled from the UAE to Turkey, Qarshi (Uzbekistan) where all the tanks were emptied and then transported from Qarshi to Poti Port (Georgia). The final leg of the journey had the cargo transported to Antwerp in Belgium.
Despite the challenges KGE Baltic faced including arranging logistics at a variety of ports, as well as moving dangerous goods across sea and road â along with their approvals â the tanks were safely delivered.
KGE Baltic covered the entire process such as the movements of cargo and survey reports alongside DGR approvals. All the materials were emptied in Qarshi and required cleaning certificates along with all the usual formalities.
âOnce again KGE succeeded to handle this project with complete professionalism and customer satisfaction.â
The post KGE Baltic nominated for ISO tank shipment appeared first on Project Cargo.
Hellmann Worldwide Logistics is opening a new warehouse location totaling 18,000 mÂČ in Oelde, Germany, from which it will ensure production supplies to the worldâs largest CLAAS plant in Harsewinkel.
Initially, the logistics provider is putting 9,000 mÂČ of warehouse space into operation, with a further 9,000 mÂČ to be occupied later this year following the completion of the second construction phase. With this significant capacity expansion, Hellmann is responding to the ongoing growth of CLAAS, the leading international manufacturer of agricultural machinery. The opening ceremony of the new warehouse, which is one of the largest Hellmann locations in Germany, was attended by the management of CLAAS and Hellmann as well as the Mayor of Oelde.
Hellmann rents the newly built procurement warehouse for components from India, Turkey, and China exclusively for its long-standing customer CLAAS. In Oelde components ranging from screws to 120-kg drum gearbox for combine harvesters and forage harvesters are stored, packed, picked and shuttled to the production plant several times a day. The new site features state-of-the-art warehouse technology and a sustainable design. For example, Hellmann operates a 9,000 mÂČ photovoltaic system on the hall roof to cover part of its energy needs.
âFor years, Hellmann has been an important and strategic partner in the context of our European land transports and our global air and sea freight. In autumn 2018, we were able to expand our cooperation to the area of contract logistics by commissioning the site in Oelde. In addition to the initial pure warehousing activities, the order spectrum has been expanded to include picking and sequencing scopes. Hellmann thus forms an important part of our supply chain and our immediate production supply. We are pleased to shape growth together at the new location in Oelde accompanied by significant process improvements,â explains Bastian Linnenbrink, Head of Supply Chain Management, CLAAS Self-Propelled Harvesters.
âCLAAS and Hellmann are linked by a very unique success story: Over the past ten years, we have continuously expanded our cooperation, so that today, in addition to contract logistics, we are also active in all other logistics areas for CLAAS. With the new warehouse, we will be able to sustainably build on these successes to continue growing together with CLAAS and, of course, to create and secure jobs in the region,â says Volker Sauerborn, Chief Operating Officer Contract Logistics, Hellmann Worldwide Logistics.
The post CLAAS and Hellmann expand strategic cooperation appeared first on Project Cargo.
Vestas has received a 104 MW order for the Pinta y Guindalera wind park, to be located in Valladolid, Castilla y LeĂłn, Spain.
The contract includes the supply and installation of 23 V150-4.5 MW wind turbines, as well as a 10-year Active Output Management (AOM 4000) service agreement.
The order has been placed by renewable energy producer Estudios y Proyectos Pradamap, SLU (Grupo Vapat). The company has developed 650 MW of wind power plants, which are currently in operation in Spain. At present, Grupo Vapat is developing 1,000 MW of additional renewable capacity in the country.
Building on the commercial success of the V150-4.2 MW wind turbine, the V150-4.5 MW delivers an increased annual energy production with an expanded global market applicability.
âWe would like to thank Pradamap (Grupo Vapat) for the trust placed in Vestas 4MW platform and one of its latest models. Its full converter technology provides our customers with the reliability they need to to operate in the Spanish grid, marked by an increasing participation of renewable sourcesâ, says AgustĂn SĂĄnchez-Tembleque, Vestas General Manager Spain & Portugal.
Turbine delivery and commissioning are expected in 2023.
The project will also benefit from Vestasâ strong footprint in Spain. The company manufactures V150 blades at its blade factory in Daimiel (Ciudad Real), both for the 4 MW and the EnVentus platforms. Since 1991, when Vestas installed its first wind turbine in Spain, the company has achieved over 5 GW of installed capacity, corresponding to 130 wind parks in the country.
The post Vestas receives 104 MW order in Spain appeared first on Project Cargo.
Project Logistics Allianceâs Malaysian member MS Global Freight Solution Sdn. Bhd, recently moved equipment for oil & gas from Port Klang to Kuching, East Malaysia door to door.
The largest unit was 1200 centimetres in length, 225 centimetres in width, 330 centimetres in height and weighed 18 tons.
The over-length and over-height item had initially been booked on a flatbed container, but sailing was delayed for 20 days due to port omission. The company had to find an alternative option urgently since the shipment had a deadline. Opportunities to carry oversized cargo to East Malaysia are limited, but they found an option with the RORO vessel. They planned and monitored trucking and lifting carefully since cargo was sensitive and high value. The item arrived at the consignee timely and safely, and their customer was satisfied with the service.
MS Global Freight Solution Sdn Bhd, located in Port Klang, Johor Bharu (Pasir Gudang) and Penang, Malaysia, can handle sea and air heavy lift project cargo from/to Malaysia including East Malaysia such as Labuan, Bintulu, Kota Kinabalu, Kuching. The company provides feasibility study, road survey, method of statement, execution, and supervision of packing, transportation, loading, lashing, unloading, and placement at the consigneeâs site. They arrange breakbulk and RORO vessels, open top, and flat rack containers and maintain a close relationship with many vessel operators.
The post MS Global completes shipment to Kuching appeared first on Project Cargo.
On September 8, in Le Havre, about 300 students, professors-researchers and partners from the engineering school of Le Havre Normandy University attended the presentation of innovation and educational projects labeled by ISEL (Institut supĂ©rieur dâĂ©tudes logistiques), as part of its LOGIN (Logistics Innovation) chair.
BollorĂ© Logisticsâ BIODIV was thus presented by ValĂ©rie Pira, CSR Manager and Biodiversity Referent for the company. This two-year mission aims to study the impact and the margins of progress in terms of the preservation of biodiversity for the companyâs transport and logistics activities throughout its value chain.
In the logic of life cycle analysis, how can we better quantify and qualify the impacts of the activities of the company, its customers and suppliers on biodiversity in order to have a global vision of them all over the world? What methodology accepted and recognized by all stakeholders should be applied for this sector, like the carbon footprint, to meet climate challenges?
With the support of Laure Frémeaux, from the ecological consulting firm Elan, the CSR Department of Bolloré Logistics with its Biodiversity Committee and the teams of biodiversity referents and ambassadors will work on this innovative subject in partnership with research professors from the LOGIN chair, a space for reflection and innovation for the logistics of today and tomorrow, whose objective is to create interaction between the projects of partner companies and its educational lessons.
The implementation and monitoring of BollorĂ© Logisticsâ biodiversity policy on its buildings labeled BiodiverCityÂź and certified Biodiversity Commitment by Ecocert since 2015 have made it possible to identify interesting actions that can be duplicated in its international network, in particular via the internal AcTogether challenge.
The objective is to ensure that as many of the companyâs agencies as possible gradually implement local action plans in order to respond to the companyâs priority challenges with regard to biodiversity (preservation of biodiversity in its offices and hubs, reduction of the impacts on biodiversity of its activities, the activities of its customers and the activities of its suppliers).
Named a Company Committed to Nature in 2021 by act4nature France, an initiative led by the French Office for Biodiversity, Bolloré Logistics is strengthening its policy in favor of biodiversity with specific voluntary commitments from the Powering Sustainable Logistics CSR program deployed internationally at horizon 2025.
The post Bollore BIODIV Project unveiled at launch of LOGIN appeared first on Project Cargo.